After a wheel has been created, pressure is applied to the interior barrel of the disc while it is rotating, resulting in formed wheels. This compresses and stretches the aluminum, enhancing the wheel’s mechanical properties. When opposed to casting rims, this enables the wheel to be significantly lighter, sturdier, have better shock resistance, and have a larger load-bearing capacity.
Flow Formed wheels fall somewhere between gravity/low tension cast and completely forged wheels. Continue reading to learn more about the Flow Formed Technology, its process, pros, cons, and its methodology to answer your question of what are flow form wheels.
Flow Forged Technologies Wheels
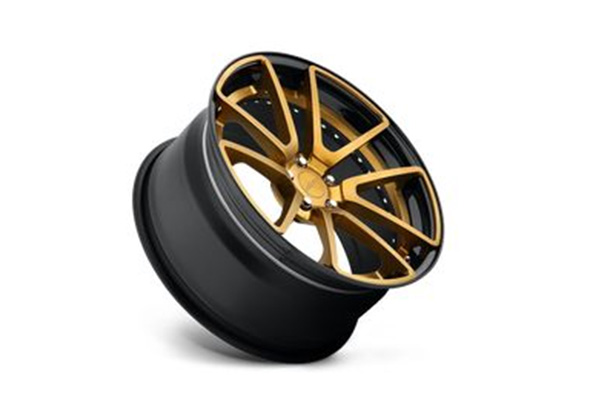
Flow Forged technique is a process that involves turning the wheel’s materials on a mold at a fast speed and forming the wheel with hydraulic steel runners under constant pressure. This pressure causes the metal to conform to the mold’s shape, resulting in the wheel’s structure.
Process
The disc is cast like every cast wheel, however, the press for the cylinder component of the wheel is thinner than the completed wheel will be. After the cast is completed, the completed wheel is put on a device and warmed to nearly 400 degrees before being spun.
A rotating disc makes contact with the wheel and stretches the barrel, giving it its ultimate shape and breadth. The aluminum in the barrel component of the wheel is strengthened by this hot-press treatment.
The flow-forming procedure can result in extremely light wheels.
Flow Forged vs Forged vs Cast
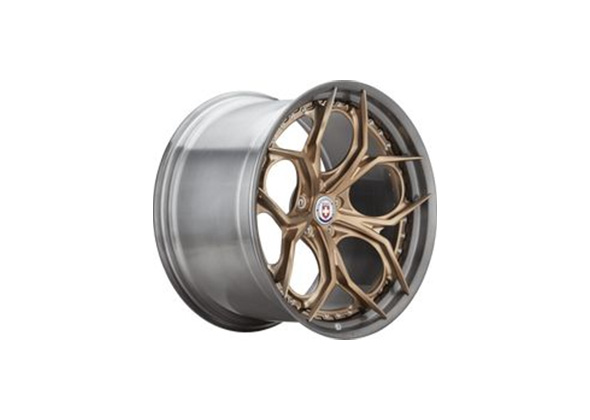
The most prevalent manufacturing procedure for rear wheels on the market is casting aluminum wheels. These wheels are created by pouring molten aluminum (or drawing it in with a suction) into a mold that shapes it into the required wheel shape. After the aluminum has cooled, the completed wheel is cut, drilled, and clipped.
A cast wheel has the advantage of being relatively affordable. The breaking point of a forged wheel is one of its drawbacks. Cast wheels have a tendency to shatter under pressure and have dramatic track failures. Because of the alloy’s permeability, the casting has the potential to break aside.
When traveling, this is a negative thing that may do a lot of damage, to not just the wheel but also to the rest of the automobile as well.
Flow Forged wheels begin as a casting wheel that is fed into a device that rapidly rotates it while iron rollers exert pressure to stretch the cylinder downward. Because the aluminum in the barrel is squeezed and twisted at the same time, it boosts the barrel’s tensile qualities, making it extremely similar to a completely forged tire.
Forged wheels are durable and lightweight, but those advantages come at a cost. Forged wheels are, without a doubt, pricey. When you look about how these tires are manufactured and how much metal is required, it’s easy to see why they cost so much.
Forged for sturdiness, Forgeline wheels start with a one-piece unit that works. To make room for the powerful wheel, a lot of forged samples are taken.
This method produces a lightweight wheel with a high load rating.
Pros and Cons of Flow Forming Rims
Let’s discuss the pros and the cons of flow forming rims.
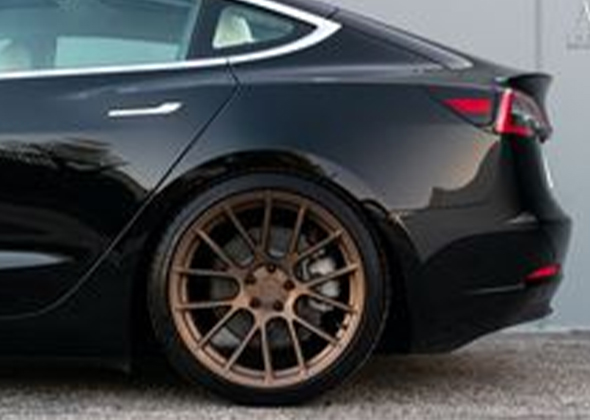
Pros:
- The disc weighs much less than a conventional cast tire with the same spec due to the flow forming technique. A Flow Formed Wheels reduced weight allows for greater power delivery and increased power. Furthermore, the Flow Formed Wheel saves money by reducing fuel use and increasing mileage.
- Flow Forming Technology not only makes the wheel lighter but also makes it stronger.
- When compared to a traditional cast wheel, Flow Formed Wheels produce a 20-30% improvement in compressive strength in general. When driving a vehicle, this provides additional resistance properties.
- As previously stated, one of the main advantages of the tougher is its increased shock resistance. The higher stress capacity created by the expanding and squeezing of the original cast wheel is enhanced with Flow Formed rims.
- Elongation is also known as the maximum amount of flex a tire can withstand before shattering. Flow Forming Technology enhances extension in the cylinder and rear plate areas, greatly increasing shock resistance in the event of a possible threat.
- Because Flow Forming Technology raises the mechanical properties of a wheel, it also offers a higher load rating than a traditional cast wheel.
Cons:
- Because the core of the tire is still a forging molded cast, it is likely to fail.
- It is less durable than forged wheels.
Applications of Flow Forming Wheel Rims
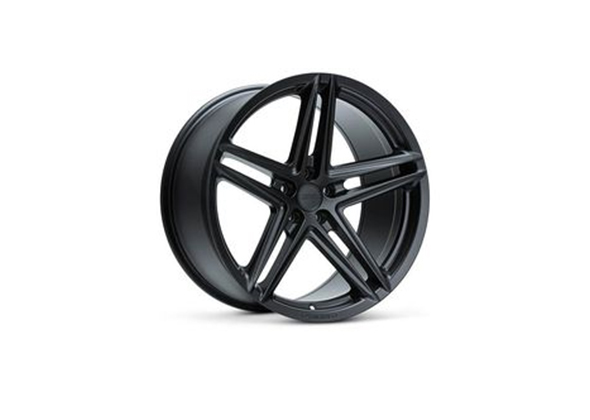
Many people are drawn to rims due to their attractive appearance. You can make a new appearance by changing the style or size of your rims. Larger rims give a car a muscular or sporty appearance, and smaller rims give it a low-profile appearance.
A car’s wheel rim is an essential component. Its primary functions are to assist in drive systems on the roadway and to resist vehicle weight and practical situations like turning and stopping, as well as environmental factors.
Rims are useful for more than just making your car look fantastic. A nice pair of car rims will improve the performance of your car and give you a smoother ride.
Changing the thickness of the car’s rims has an effect on its equilibrium, handling, braking, and speed, and also the speedometer’s accuracy.
Conclusion
One of the most modern manufacturing methods to approach the wheel business is flow forming. The transmission of pressure to the inner cylinder of the disc while it is rotating and after it has been tried to cast is referred to as Flow Forming Tech. The aluminum is stretched and compressed throughout this process, increasing its tensile strength.
The procedure has features that are similar to those seen in the workpiece in this regard. In comparison to normal cast wheels, the finished result is lighter, stronger, has enhanced elasticity, and has a significantly higher shock resistance as well as a higher load capacity. If you need to know more info about car wheels or want to start a car wheel business, contact Sunway Autoparts.